Borla Gomma was born in 1970 from Borla Industries’ need to have a pierceable rubber fitting for transfusion kits. The company begins to produce small quantities of fittings and caps for use in the medical field. Today Borla Gomma produces more than 500,000,000 pieces.
Who we are
Over the years the company has always invested in technology, obtaining qualitative results capable of meeting the requirements required by the leaders of the medical sector.
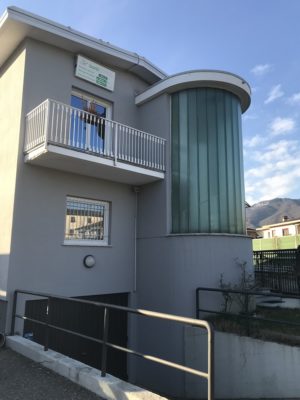
Our company
Borla Gomma has its own injection molding technology: with modern machines and an innovative molding technology, Borla Gomma can offer high quality components at a competitive price, placing itself among the leading companies on the market in this sector.
Among the few manufacturers in the world, Borla Gomma has developed a Latex-free component with low release of substances, total absence of powders, absolutely MBT- and Nitrosamines-free.
High quality, due to conformity of all products to:
- European Pharmacopoeia (Eur.Ph.IV Ed.)
- ISO / DIS 8536-4
- USP Class VI (plastics & rubbers)
- Biocompatibility requirements (UNI EN ISO 10993)
- Constant monitoring of production and quality control (according to UNI EN ISO 2859)
Borla Gomma is a qualified supplier of the world’s leading manufacturers of infusion and transfusion equipment.
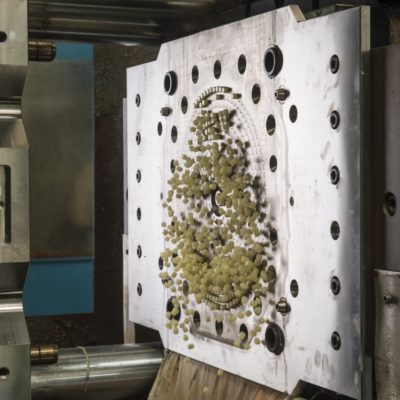
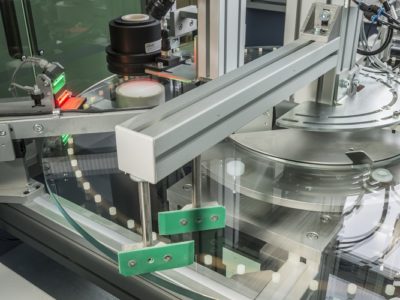
Our production
Our items for the medical components sector are produced with compounds specifically developed for the application, which together with a level of quality and compliance, allow us to be a supplier to the major manufacturers on the market.
The compounds are latex free and comply with European Pharmacopoea regulations, with a production process validated and entirely carried out internally that allows us to have control and traceability of all phases, from raw materials to shipping. Needle points available in different designs, inerts, excellent self-closing, low permeability and resistance to penetrability.
The designs are in accordance with international standards. Different types of compounds are available in compliance with a wide range of medicines and product specifications, available for urological terminals, needle points, disposable drip connectors, transfusion and hemodialysis items, syringe pistons. Distributed with a final treatment with silicone on specific customer request, and packed in a clean room.
Quality
Quality
Our Quality System starts from a list of primary suppliers, selected and approved, we only use raw materials with a high level of quality. A “one way” line and a “batch to batch” production process allow us to have detailed and documented traceability. Throughout the production chain and for each phase, an intensive quality system is assured. All the items produced, per single batch, are at the end of the production line meticulously checked by our QC before being available for shipment. The production documents of the individual lots are kept for years for our traceability together with the counter-samples of the lot / shipment. A dedicated MES system automates and consolidates our Quality system. In the production departments, we ensure our attention to all aspects of hygiene and cleanliness. Our employees play a key role in our organization, Borla Gomma is oriented towards their professional growth, letting them work in a safe and healthy environment.
“Zero” flaws philosophy
A zero defect philosophy With many decades of experience in the production of highly critical components for a variety of markets, Borla Gomma has developed systems to support our zero defect production philosophy. Let’s start with the quality approach based on the design, according to which the processes and products are designed according to a zero defect philosophy and employ automated processes as far as possible. If necessary, we can combine this process with inspection technology that guarantees 100% control of every single part in your application.
Already in 1995 we were at the forefront with our first fully automated camera inspection system for rubber products for the Japanese medical market. Since then, we have consistently based on this experience and are currently using our fourth generation camera systems in a class 100 clean room. It is thanks to this combination of exceptionally consistent and robust automated processes with detailed inspection tools that we can provide our customers millions of pieces per year, each of which meets the requirements of a high quality product that you have come to expect
News
Contacts
Address: Via Tividino, 15 - 21020 - Casciago (VA) - Italy
Phone: +39 0332 225002
E-mail: info@borlagomma.it